一、铝塑膜行业概述
铝塑复合膜(铝塑膜)是软包装锂电池电芯封装的关键材料。单片电池组装后用铝塑膜密封,形成一个电池,铝塑膜起到保护内容物的作用。铝塑膜广泛应用于各领域的锂电池中。其主要下游行业为消费电子与新能源汽车,此外也应用于军事、医疗、电动工具等相关产品中。
铝塑膜的应用领域
资料来源:公开资料整理
铝塑膜不仅是软包电池的外包装,还需要起到保护内部电芯材料的作用,因此在阻隔性、冷冲压成型性、耐穿刺性、化学稳定性和绝缘性方面均有严格要求。为了保证软包锂电池能够持续稳定运行,不产生鼓包、漏液等问题,铝塑膜需要具备极高的阻隔性、良好的热封性能、耐电解液及强腐蚀以及较强的延展性、柔韧性与机械强度等。其材料的设计、制造及应用技术都和普通的复合包装材料有质的差别,技术难度超过隔膜、正极、负极、电解液,是锂电子电池材料领域技术难度较高的环节,质量要求极高。
铝塑膜产业链示意图
资料来源:公开资料整理
目前国内主流的电动乘用车企北汽、上汽、众泰等纷纷开始尝试软包电池,2017年销量前六名的车企有四家在部分或全部车型中使用软包电池。国内动力电池企业为了满足市场需求、抢占先机,也纷纷布局软包电池。国内出货量前十名的动力电池厂商中有四家布局软包电池,其中孚能科技和国能电池以生产软包电池为主。知名电池厂商如孚能科技、上海卡耐、猛狮科技、天津捷威等均公布了5-10GWh的扩产计划,9家主流软包电池企业2017年底的软包电池产能达到27GWh。随着更多电池厂商参与到软包电池生产,2018年底软包动力电池总产能将达产能38GWh。此外,国内动力电池巨头CATL正在开发软包电池,金沙江收购AESC后将在镇江建设生产基地,未来在龙头企业的带动下,软包电池成为越来越多的新能源车企和动力电池厂商的选择,从而带动铝塑膜市场的扩大。
二、铝塑膜行业供给及需求现状
国内锂电池铝塑膜供给方面,铝塑膜产能集中度高且技术门槛较高。近年来,随着3C电子市场和新能源汽车发展迅速,我国铝塑膜一度呈现紧缺格局。中国铝塑膜市场几乎被日本企业垄断,2016年底,我国在铝塑膜产业化领域开展相关业务的企业中,大多数仍处在研发、试生产阶段,尚不具备量产能力;已经具备生产能力的企业中,产销量往往远小于生产装置产能,实际开工率低下。2016年,全国锂电池用铝塑膜产量仅494万平方米,2017年我国锂电池铝塑膜产量在900万平方米左右。2018年国内锂电池铝塑膜产量约为2023万平方米。
2012-2018年我国铝塑膜产量走势
资料来源:智研咨询整理
铝塑膜是软包装锂电池的必备封装材料,主要起到保护内部电芯的作用。软包电池安全性能好、能量密度高,已获得了国际车企的高度认可。雪佛兰Volt、Bolt、日产Leaf、福特(Focus、Fusion)等高端车型纷纷采取软包电池技术路线。国际动力电池供应商四大巨头中的AESC、LG化学也都主打软包电池。
随着消费电子领域进入成熟期,未来锂电池主要增长点来自新能源汽车领域。2018年我国新能源汽车生产约122万辆,同比增长50%,受此推动,动力电池出货量近年来也快速增长。2018年中国动力电池装机总电量约56.98GWh,同比增长56%。,2018年新能源汽车软包动力电池装机总电量约7.62GWh,同比增长63.5%,占整体总装机电量的13.4%。其中装载在新能源乘用车上约5.10GWh,占比66.9%;在新能源客车上约1.43GWh,占比18.8%;在新能源专用车上约1.09GWh,占比14.3%,仍有很大的提升空间,动力领域的发展成为软包电池发展最大的推动力。
三、铝塑膜竞争格局
锂电池一般由正极、负极、电解液、隔膜以及外壳五部分组成,其中铝塑膜因为技术难度高,国产化程度不及其他部分,多年来大量依赖进口。2017年全球铝塑膜市场中,大日本印刷(45%)、日本昭和电工(29%)、日本凸版印刷(12%)占据主要市场份额。
国际铝塑膜主要企业
资料来源:公开资料整理
随着3C、储能、动力领域所用锂电池拉动铝塑膜需求持续增长,同时材料进口导致成本居高不下(毛利率一度高达60%),铝塑膜进口替代有迫切需求,因此越来越多的国内企业将目光投注于该领域,包括道明光电、紫江新材、新纶科技、苏达汇诚、东莞卓越、珠海赛纬、佛塑科技、明冠新材、连云港申元等超15家企业均已进军铝塑膜市场。2017年国产铝塑膜占比约10%,较2016年的4.5%有一定提高。
国内铝塑膜主要企业分析
地区 | 名称/简介 |
道明光学 | 自主研发铝塑膜干法工艺,现行2套生产线满产产能达1000万平方米/年;2017年获得超三十家3C锂电池企业订单,动力类铝塑膜已通过部分企业测试并进行小批量送样 |
东莞卓越 | 主要生产113μm与88μm的消费电子铝塑膜,动力电池用铝塑膜产品推广中;自主研发热复合工艺与二次复合工艺,自主开发特种CPP材料 |
佛塑科技 | 铝塑膜项目于2008年开始立项,2009年至2011年初完成产品结构设计、关键性能的突破,2012年开始试产送样评测,2013年开始小批量进入市场销售 |
明冠新材 | 承诺7月初铝塑膜产能达5000万平方米/年;铝塑膜相关专利40余项,6项产品经国家权威机构认定达到国际先进水平 |
苏达汇诚 | 从日本引进成套锂电池用铝塑膜生产设备及相关技术人员,目标2018年实现3C铝塑膜月销量100万平方米以上、动力电池用铝塑膜月销量50万平方米以上 |
新纶科技 | 2016年收购凸版印刷持有的铝塑膜生产业务及相关技术专利,产能达200万平方米/月;2017年开启常州二期项目,其中铝塑膜项目一期月产能300万平方米,已于2018年6月量产,铝塑膜项目二期月产能300万平方米,预计2019年3月量产. |
紫江企业 | 产品已通过ATL、光宇、力神等大型锂电池厂商认证,产能达1500万平方米/年;2016年铝塑膜产品数码与动力结构占比为9:1 |
上海恩捷 | 2018年投资建设5条铝塑膜进口生产线苏州锂盾主要生产3C类电池用铝塑膜,已有小批量送货 |
赛特新材 | 2018年总投资12亿元的铝塑膜生产项目落户福建连城,项目分三期实施,满产后产能达5000万平方米/年 |
安德力 | 2014年引进两条日本铝塑膜生产线,满产产能达3000万平方米/年;采用热法工艺,主要面向3C电池领域 |
资料来源:公开资料整理
四、国内铝塑膜行业主要问题分析
国内企业已逐渐在铝塑膜技术上取得进展与突破,虽因产品性能与质量与国际化标准尚有一定距离,目前国产铝塑膜产品主要面向消费电子领域,但已有部分企业逐渐布局动力电池用铝塑膜,并开始批量供货。预计未来在新纶科技、道明光学等龙头企业的带领下,国产铝塑膜企业在使用材料、技术工艺、机器设备等多个方面均会不断完善,铝塑膜产品在质量、性能上有望获得提升,进口替代势头渐盛。
客观来看,铝塑膜国产化的关键。在技术,一旦技术实现突破,国产铝塑膜产品相比海外企业在定价上将具备绝对的优势,国产铝塑膜在原材料价格(主要是铝箔)方面存在显著优势,国产铝塑膜在价格上同样比进口产品低约20%。由于目前我国铝塑膜产品的性能,只有极少数企业的几项技术指标可达到日本企业的水平,这其中存在的主要问题是耐电解液和冲深不过关:国内铝塑膜的冲深在5mm左右,国外的在8mm,甚至达15mm,总体与国外产品还有一定差距,尤其是在反应条件和精度控制上。
目前,国内铝塑膜厂商存在着以下五大困境:
1、铝箔表面处理工艺落后、污染大:由于采用水洗出油和“铬酐”钝化处理,污染大。同时,由于水有表面张力,导致铝箔微孔中的油无法清洗干净,导致后续工序产生缺陷。
2、铝箔的水处理工艺会产生“氢脆”,因此勿国产铝塑膜耐拆度差。
3、铝箔表面涂布UV层、铝箔挺度不够、干式法复合时易褶皱、宽幅产品无法制作且良率差。
4、对于CPP,国内主要采用淋膜机淋涂,与高导热的铝箔表面复合时,易卷曲、产生层状结晶。
5、由于国内胶粘剂配方技术原因,导致产品易出现分层剥离问题。
相关报告:智研咨询发布的《2019-2025年中国铝塑膜行业市场潜力现状及投资战略研究报告》

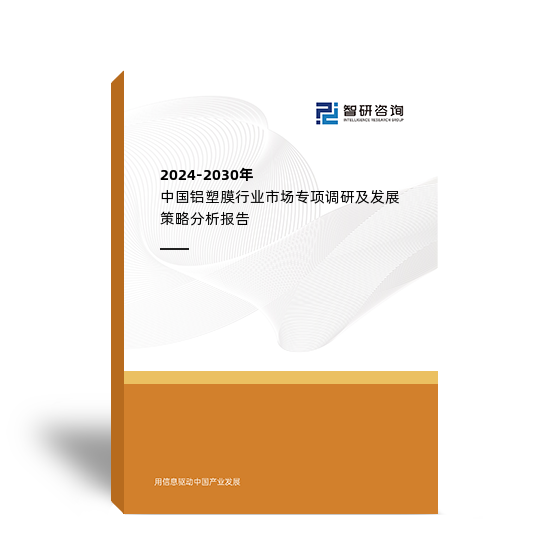
2025-2031年中国铝塑膜行业市场专项调研及发展策略分析报告
《2025-2031年中国铝塑膜行业市场专项调研及发展策略分析报告》共十四章,包含2025-2031年铝塑膜行业投资机会与风险,铝塑膜行业投资战略研究,研究结论及投资建议等内容。
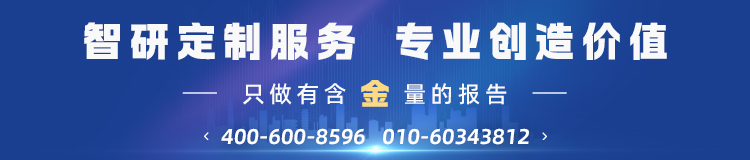
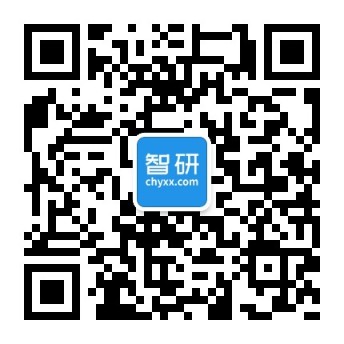
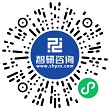
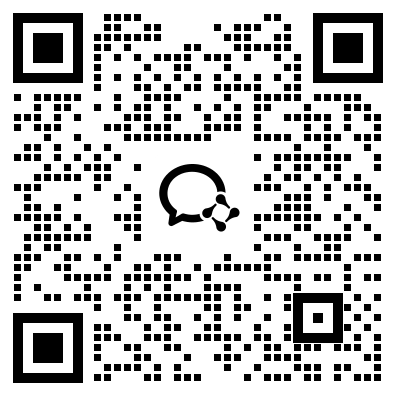